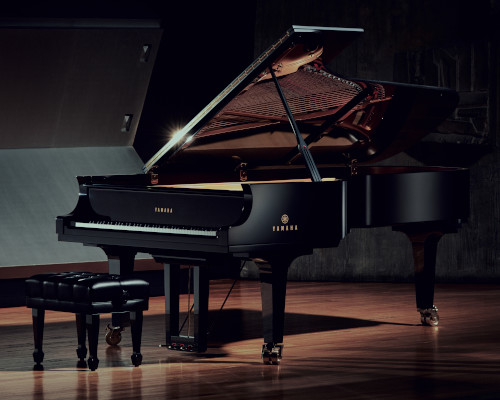
Yamaha CFX Concert Grand Latest Release
I used to have a teacher who would frequently say, “For every single grade point PAST 80%, it takes as much effort as the FIRST 80.” I believe this statement to be true from experience. The first 80 is the easiest. Chipping away at every point past that is the challenge. The bulk of the work can bring a project into shape but it’s the pursuit of excellence, that’s where the challenge lies.
Yamaha is one such company that dedicates substantial commitment in resources to consistent research and development to refine their pianos. What’s interesting to note and what I’ve begun [...]
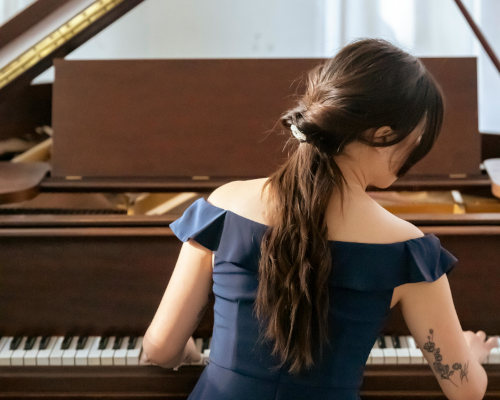
How Much Is My Piano Worth?
The value of a piano is obvious ~ it’s the music that you make with it. But often, families are going through life changes which involve a house move and unfortunately, the piano needs to be sold. They invariably ask the question, “What are we going to do about the piano?” This question comes up because, as you can imagine, they’re not easy to move. We don’t simply pack them away in a cardboard box with the rest of our belongings. We live in a world in which monetary value is attached to objects. And despite the fact that it’s [...]
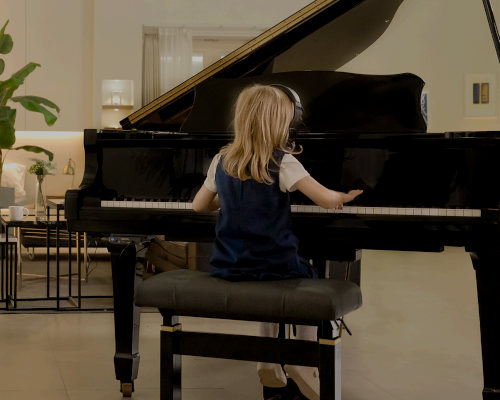
Retrofit Silent Piano Systems
You’ve been playing your piano for years now and the time has come to seriously consider downsizing the house and move into a condo. But what do you do with the piano? You love your piano and can’t imagine life without it and besides, you absolutely hate the idea of playing a digital keyboard. Many people don’t know that you can add digital functionality without compromising your existing piano. Yes, it is completely possible to keep your piano AND add silent features so that you can use headphones and not hear the hammers strike the strings. Although this technology is [...]
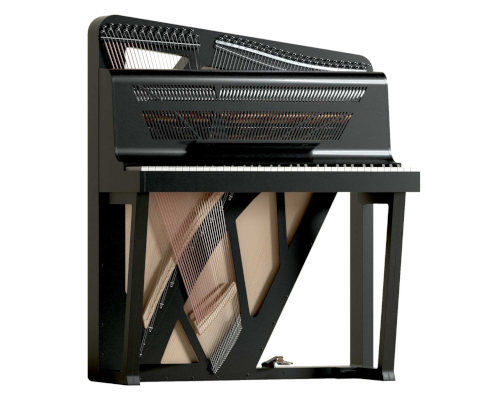
Keybird ~ A New Portable Piano
Many years ago, I remember seeing a piano in a museum similar to the one shown above (built in 1787 by Christian Gottlob Hubert. On display at Germanisches Nationalmuseum – Nuremberg, Germany). I have often wondered why acoustic portable pianos never really took off. Although we’ve seen more portable keyboard instruments like harpsichords, accordions or electronic keyboards, they operate completely different from a traditional piano in that they either pluck the strings, use air with reeds, or play back a recording to create sound. This is unlike a real piano that utilizes mallets to strike the strings. But when you [...]
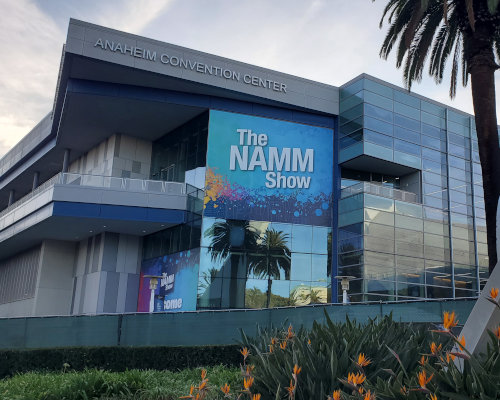
NAMM 2024 in Review
This was the first year since covid that the National Association of Music Merchants (NAMM) trade show was back to its regular January date and, in fact the first show where it felt back to normal. How was it? To answer that, I’m going quickly review the piano market over the last few years. Piano sales boomed during covid. Think about it – everyone was at home and with time on their hands, many turned to hobbies to fill the isolation. Piano stores sold most everything they had but replenishing stock and fulfilling backorders was challenging as many factories were [...]
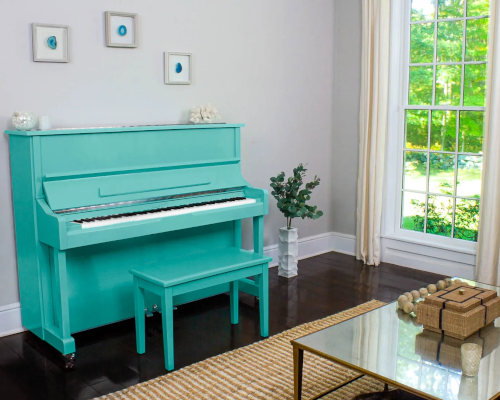
Buying A Piano Online?
I’ve often wondered when the business model of piano buying would start to change. It seems like we feel comfortable purchasing everything from toothpaste to tires online and yet pianos are one thing that you still buy in a store. Well some of that is about to change. After speaking with Larry Caruso from Caruso Piano, they’re launching a brand of piano made specifically for online ordering. It’s called Sonnova. I recently had the pleasure of speaking with Larry Caruso and Brian Biddle about their new brand but also this new method of piano buying.
Glen Barkman (GB): Larry, how did [...]
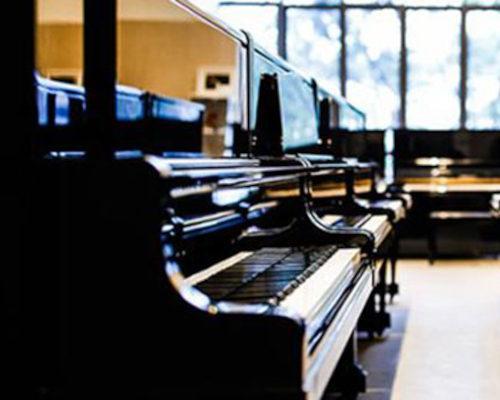
How To Buy A Piano
The thought of buying a piano can be exciting but it can also be a bit intimidating or daunting, especially if you don’t know anything about them. But have no fear, because at Piano Price Point, we’ve compiled so much of the data and written articles to make your job easier.
To narrow down the scope of buying a piano, you first need to decide what kind of piano you’re looking for. Ask yourself these three questions:
Are you looking for a grand or an upright piano?
Are you looking for new or used?
What’s your budget?
A grand piano is one where the strings [...]
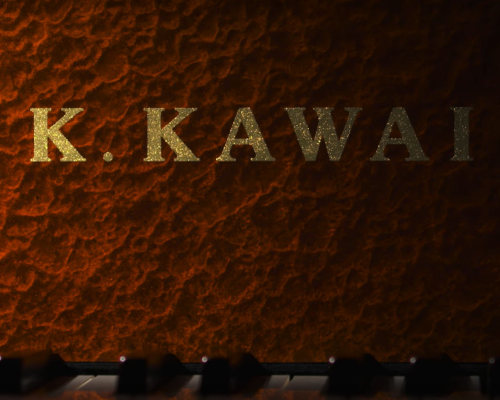
Kawai America Celebrates 60 Years With Ancient Lacquer Tradition and Pure Gold Dust
Money, apparently does grow on trees or at least in ancient times it did. It’s been recorded that rare tree sap was used as a form of payment for tax because it was deemed so valuable. This sap from the tree was harvested and refined into lacquer with incredible clarity and sheen. Many thousands of years ago, it was reserved for imperial palaces, religious temples and shrines. Early examples have been dated to 7000BC. It has been considered almost a wonder of nature – when cured, this lacquer is almost impermeable to the elements. In Japan, where these trees grow, [...]
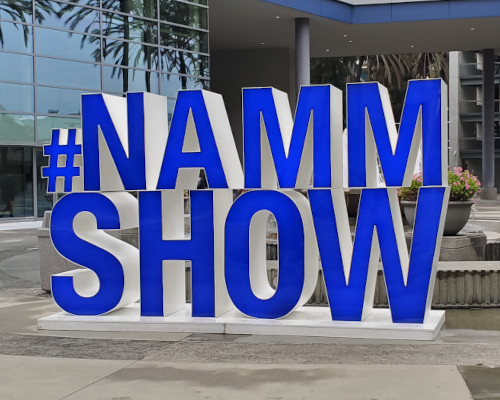
NAMM 2023 Piano Review
NAMM is always a great time to see the latest pianos. This was my first show since covid and despite being off-schedule in April (the show usually runs in January), it was nevertheless well represented. Many of the manufacturers opted out of this show because the upcoming show in 2024 is only 9 months away. These shows are a massive amount of work for presenters. When you think of how many pianos get moved and tuned, you can appreciate how much coordination and personnel are required to put together a booth and understandably, some manufacturers didn’t wish to present twice [...]
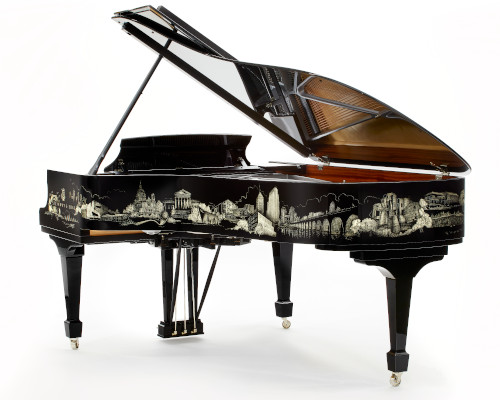
Steinway Presents The Skyline Collection
The term “art case” refers to a piano cabinet that has been visually enhanced. Historically, pianos were often owned by aristocrats and royalty, their appearance mirrored the opulence of a palace or echoed the trends of the day. They often featured exotic cuts of wood or intricate carvings. But as the piano has become more mainstream, so the cabinetry, more simplified. Today, when we think of a modern piano, we perhaps think of a shiny black grand on a concert stage with smooth lines. In fact, the vast majority of pianos manufactured in the world today are finished in high [...]
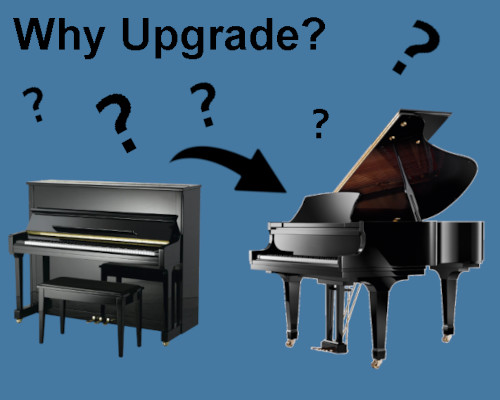
Why Upgrade From An Upright Piano To A Grand Piano?
I’ve heard this statement many times. In fact it happened when I was a young. The piano teacher states, “Your children are at a level now where it would be helpful to have them practice on a grand piano”. But is there any substance to this statement? Is there validity in upgrading to a grand piano? Is there empirical data that proves the advantages of a grand piano? In short, the answer is yes. Let’s take a look at what makes grand pianos so… grand! There are 5 main differences between upright and grand pianos.
First, grand piano keys are [...]
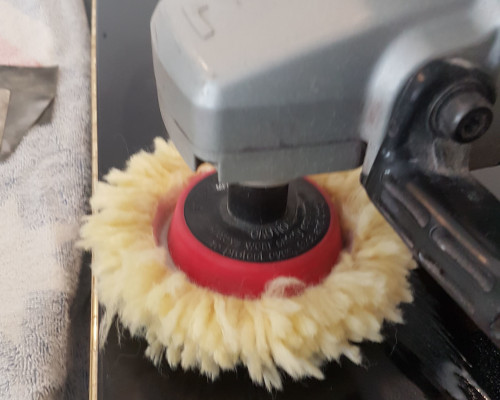
How To Remove Scuffs and Scratches from Pianos
It’s inevitable that pianos will get bumped, scratched and scuffed. High polish finishes are like mirrors and when something unfortunate happens, it can be not only disappointing but daunting to know how to remedy the situation. In this 2-part series we are first going to investigate removing scuffs and hairline scratches and then in the second part, we’ll look into chip and deeper scratch repairs.
Disclaimer: while this presents one solution to repairs, this is by no means exhaustive. It is just one method that I have found to be successful over years of working with pianos. If you don’t [...]
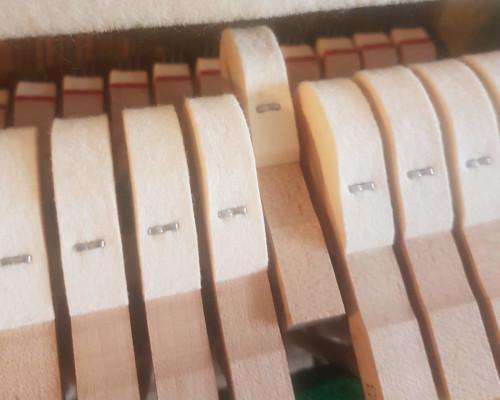
Why Do Piano Keys Stick?
Aside from tuning the piano, there’s one question that gets asked more than any other. “Can you fix a sticking key?” The term ‘sticking key’ refers to a mechanical failure where a piano key is depressed and it doesn’t return to its normal position in a timely manner. It can happen on new pianos and old pianos alike and today we’re going to examine the main reason why piano keys stick.
F stands for Friction
The vast majority of the problems with a sticky piano key come from unwanted friction. That friction shows up in four forms: blockages, wood swelling, joint corrosion, [...]
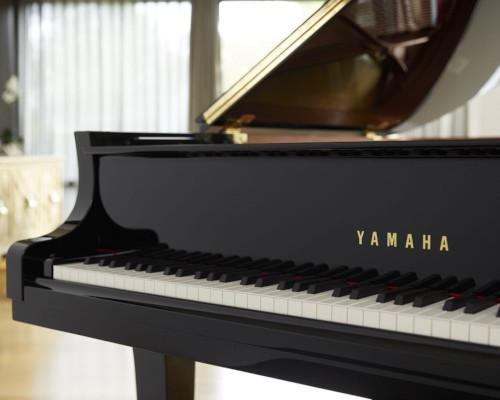
Five Tiers of Yamaha Grand Pianos
It may be difficult to wrap your head around the fact that Yamaha has five different tiers of grand pianos. Growing up I only knew of the famous C series grands. The Conservatory (letter C) followed by a number indicated the size of the grand piano. They were C1, C2, C3, C5 and C7. These pianos ranged in size from the baby grand 5’3” all the way up to the semi-concert grand, 7’6” in length. The concert grand, however was called CFIII. Over the years, Yamaha has transformed the C series grands and CF concert grand into 5 levels of [...]
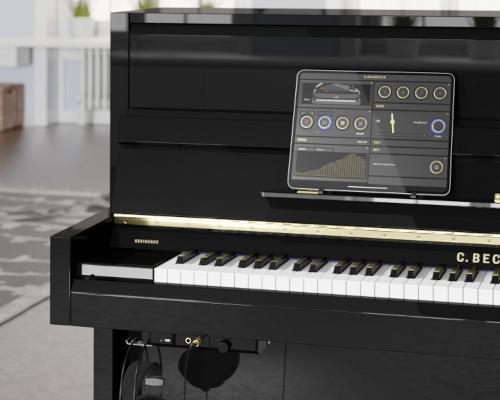
Pianos With Headphones? Big Noise About Being Quiet
Recently, silent or quiet pianos have become more prevalent in piano manufacturing. In fact, in our Virtual Piano Trade Show, it seemed that silencer systems were a very popular theme this last year. What are these pianos they call “silent”? It sounds paradoxical doesn’t it? Why make a piano that you can’t hear? And why are they making the headlines in piano manufacturing? First of all, let’s take a look at what a silent piano is comprised of. But before we do that, let’s clear up some definitions of piano types:
Traditional pianos have hammers, strings, soundboards and cast iron frames. [...]
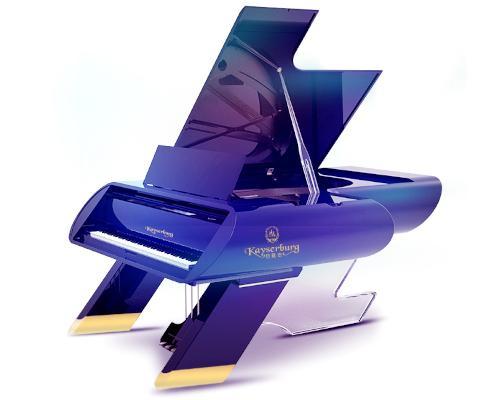
Kayserburg 3D Printed Grand Piano
It’s obvious that car makers in the 60’s were looking at the birth of air travel as the way of the future. Hood ornaments and emblems were symbols of flight with angelic creatures or airplanes. Tail-lights like jet engines were positioned on top of side “wings” and the trim, made to look aerodynamic. All of this had a purpose of course; it pointed to future thinking, an association with flight.
Just as there was a lot of talk about aviation in the 1960’s, today there’s widespread thoughts around space travel and possibly even inhabiting another planet. I don’t know if you’ve [...]
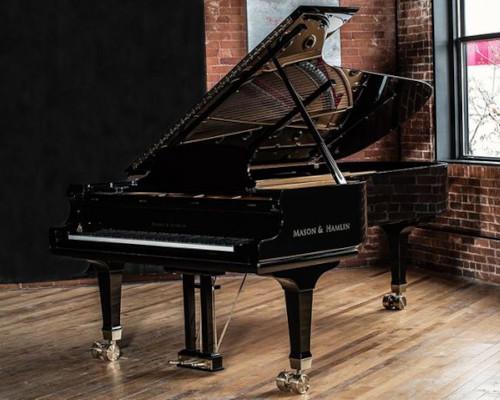
Mason & Hamlin VX-94 Concert Grand Piano Review
It’s not every day a new concert grand gets unveiled. In my mind, concert grands are the Formula 1 pianos where a company invests the very best in technology, materials and workmanship to present their utmost to the world. This year at the NAMM show (pre-covid in January 2020), I had the opportunity to play the newly released VX-94 concert grand from Mason & Hamlin.
What surprised me about this piano was the response. I guess I was anticipating a beautiful sounding and playing instrument. This piano did, in fact have both of those things in spades but what I was [...]
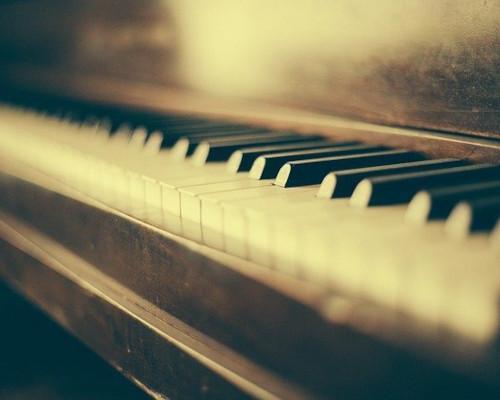
How Old Is Too Old?
Nothing beats a new piano and Piano Price Point is dedicated to delivering the news about the makers of new pianos. But sometimes they are simply unaffordable, inaccessible or possibly even discontinued and so it necessitates buying used. But that begs the question, how old is too old? At what point do pianos no longer function the way they were originally intended?
In my lifetime I’ve viewed and played several thousand pianos and as I pondered this question, it made me think about what changes occur in the lifetime of a piano. More specifically, how and why do pianos alter over [...]
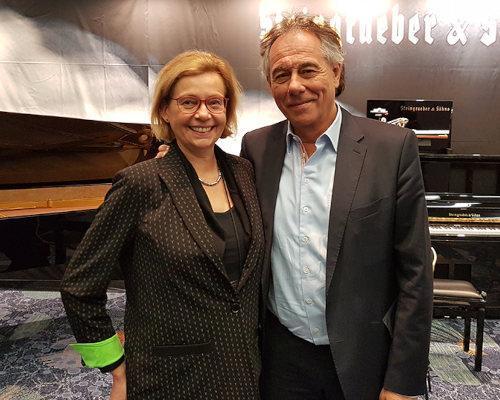
Interview with Udo Steingraeber
You don’t need to look at the artist page of Steingraeber Piano for too long before you start to realize that their pianos are highly sought after and prized by world renown pianists. It begs the question, what are they experiencing that compels them to perform on their pianos? What goes into a Steingraeber piano that sets it above others? I had the wonderful opportunity of sitting down with Udo Steingraeber at this last NAMM show in California. It was one of those unplanned, unscheduled talks which revealed much about this 6th generation piano maker and his company.
Glen Barkman: At [...]
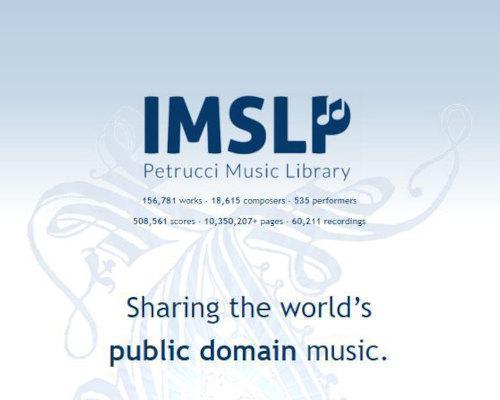
Public Domain Sheet Music
If there were one word that I would use to describe myself it’s tactile. When I’m not in the garage working on a project, quite often I’m in the kitchen and if I’m not in the kitchen, I’m doing something related to the piano. I suppose that it’s due to the fact that I like to be active and that quite often tactile activities have tangible results. One of my pastimes (I know, it’s a bit odd) is to browse recipes. If you have enough experience with cooking or baking, you can almost perceive what the end result might be [...]

Bösendorfer Secession Grand Piano
Definition: Secession – se·ces·sion /səˈseSHən/- to withdraw formally from an alliance, federation, or association, as from a political union, a religious organization, etc.
This definition of Secession piqued my curiosity as I had recently viewed the Bösendorfer piano with the same name. It’s based on this very famous building in Vienna, Austria. Why Secession? What was the need to withdraw from an organization? I dug a little deeper.
In Vienna, Austria, during the 1860’s, there were 2 main academies of art, The Akademie de Bildende Kunste (the Academy of Fine Arts) and the Gesellschaft bildender Künstler Österreichs, Künstlerhaus (Co-operative Artist House). Works [...]
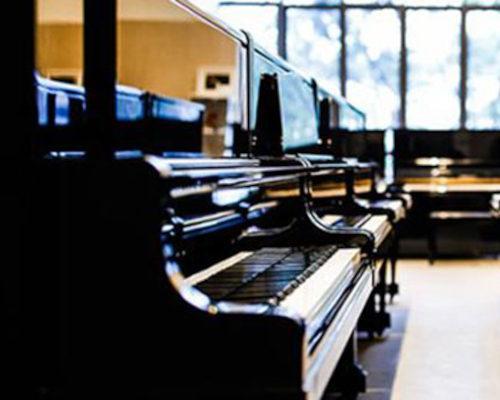
What is a House Brand Piano?
If I would ask you to name 20 brands of pianos, how would you answer? Could you name 5 or possibly 10? Maybe you can easily name 20. Historically there are approximately twelve thousand brands of pianos! It is entirely possible to encounter brands that you’ve never heard of before. I’ve been in the piano business for several decades and I am still surprised by the number of piano brands that I’ve never encountered.
House Brand or Stencilled Piano?
Piano Price Point analyzes the pianos from today’s major manufacturers. But there are many names of pianos not on this list. Who are [...]
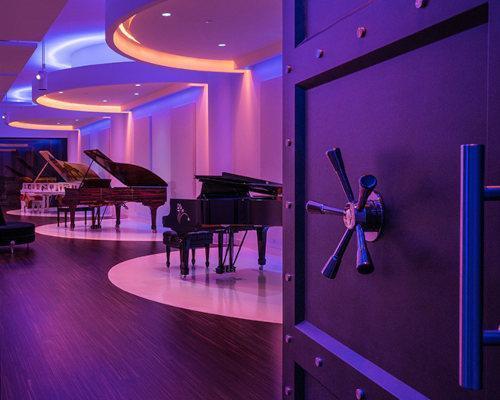
Inside the Steinway Vault
Have you heard of the Steinway Vault? Deep in the basement of the factory in New York City, the Vault houses just a handful of precious pianos worth between $200,000 and $2,500,000! But you won’t be seeing these on the next public tour. The Vault is only accessible by biometric fingerprint to 4 people at the Steinway factory.
What makes these pianos so valuable? They are all situated there for different reasons: Lang Lang, the famous Classical pianist, is one of the few artists who has worked in conjunction with Dakota Jackson (furniture designer) and Steinway artists to develop the Black [...]
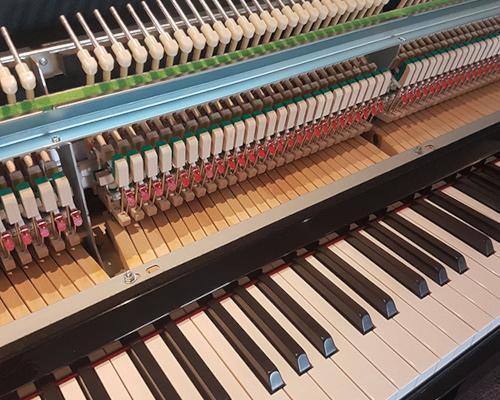
Are Hybrid Pianos the Next New Thing?
I hear a lot of talk about hybrid pianos being the next new thing and yet I believe there’s some confusion as to what a hybrid piano actually is and whether or not it can be used as a piano alternative in serious education. When we see hybrid cars driving about, from what we’ve seen in the media, it refers to an alternate power source providing some advantage in energy. While there are several kinds of hybrid vehicles, we generally assume hybrid as a gas/electric combination to power the vehicle. When it comes to pianos, hybrids refer to a digital [...]
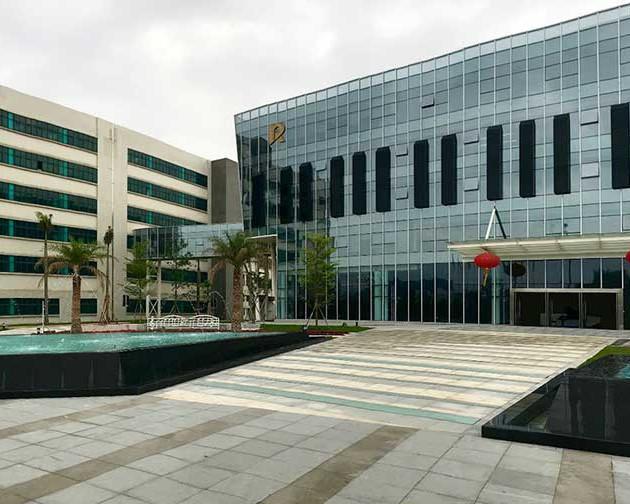
Pearl River New Factory Grand Opening
Pearl River Piano Group has grown to be the largest piano manufacturer in the world, producing more than 400 pianos per day with an annual production of 140,000 pianos. “Where do all of these pianos go?”, one might ask. Pearl River Piano dominates the Chinese piano market with an estimated 40% of the local market share. When you think about the population of China at a billion people, even 140,000 pianos represent but a fraction of 1 percent. In China, remember, the piano has really only taken hold in the last 30 years. And with the emergence of a burgeoning [...]
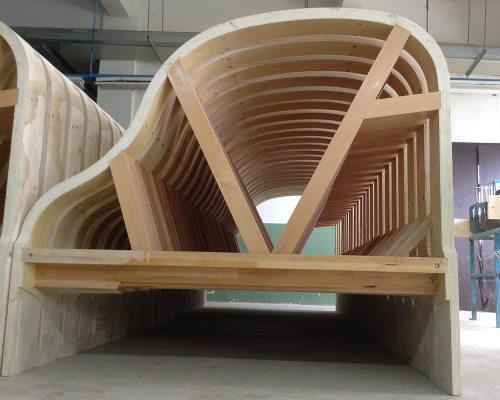
Researching Pianos ~ The Rim
Close to where I live is a sea wall made of large concrete blocks that extends out into the ocean. It serves to protect boats coming and going into the harbor. At times, the waves crash up against the sea wall and at other times, the waves bounce gently and you can see the reflected waves carry out to sea. Whenever I see these waves, I am reminded of how similar these properties are to sound and light waves bouncing off of a more rigid, reflective surface. Today’s topic is the rim of the piano. The rim is the outer [...]
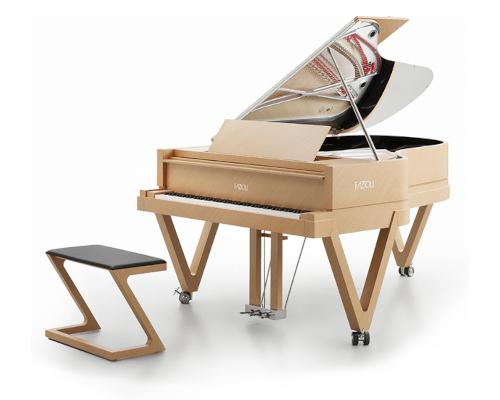
A Few Words with Paolo Fazioli
“What do the Italians offer to the world?”
I was recently in the home of an Italian dentist. We were walking through his modest but tastefully designed home, predominantly decorated in white. I followed him down a hallway as he continued.
“The Italians, we don’t have massive manpower. We don’t have natural resources. What do the Italians bring to the table?”
We entered the immaculate garage where he uncovered 2 rare Italian cars “We have style”. At this point, his gleaming white smile revealed his pride and joy.
It is no secret that Italian design is known throughout the world. From toasters to typewriters, [...]
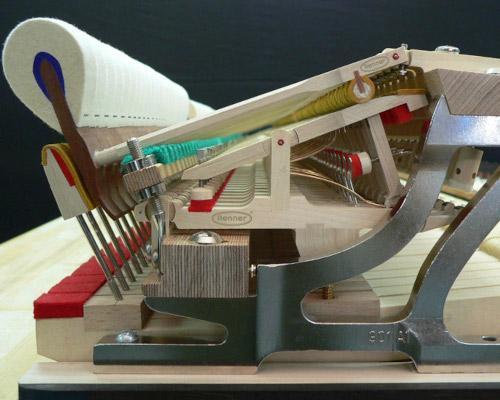
Researching Pianos ~ The Action
“I shall build an Arpicembalo!” stated Cristofori excitedly. The year was 1698 and his new invention literally translated means “harp-harpsichord”. It would be a new instrument that would sound like a harp and have keys like a harpsichord. Harpsichords have plucked strings but this new invention would have mallets that strike the strings. It was described in the inventory of the Grand Prince Ferdinand de Medici, his employer as ‘an instrument that could produce both soft and loud tones with 2 sets of strings at unison pitch having a cypress soundboard’. Needless to say, the Arpicembalo name didn’t last but [...]
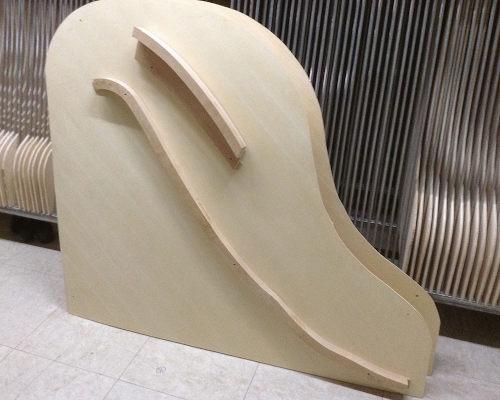
Researching Pianos - The Soundboard
When doing research on pianos, what role does the soundboard play? After a key is struck on the piano, the hammer is activated to strike against the strings. The vibration of the strings, in turn transfers the vibration through the bridge to the soundboard. It’s the job of the soundboard to act as a transducer, transforming the vibrations of the strings into audible waves of sound. While we casually talk about the soundboard being an amplifier, technically speaking an amplifier ADDS energy to multiply the sound source whereas a soundboard inherently transforms and radiates energy into sound waves. If you [...]
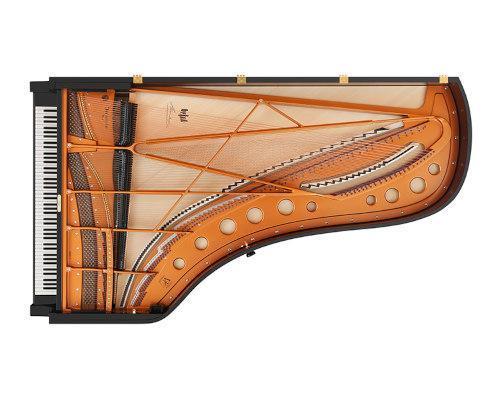
Bösendorfer Vienna Concert Pianos
They say that French cuisine and baked goods are inseparable from the ingredients grown there, that the quality of the food is due in part to the local culture from farm to table. In music, there is something similar in Austria known as the Viennese sound. It is a unique sound that is also considered inseparable to the culture. In fact, there are instruments named Viennese because they are actually constructed to produce tones in keeping with Viennese sound. So what is that sound? After visiting Vienna briefly, you gain somewhat of an understanding but it takes the experience to [...]
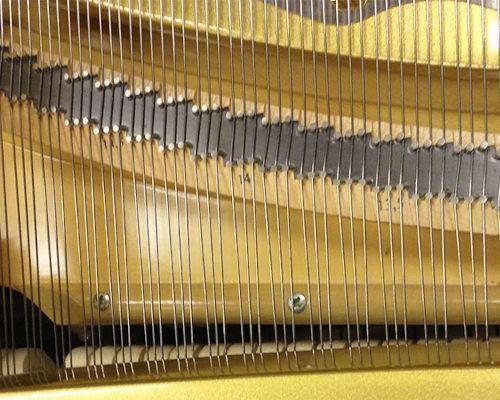
Researching Pianos - The Bridge
In the last 2 articles, we examined the hammers and strings, which are primarily responsible for the initial impact of piano tone. But tone without amplification will not be heard. If you’ve ever listened to an electric guitar that is not plugged in, the sound of the strings is very faint. That’s because they do not have natural amplification from the soundboard which magnifies the tone. This month, we’re not going to look at the soundboard, however but the intermediate piece that transfers the tone to the soundboard. The part responsible for this is called the bridge because it acts [...]
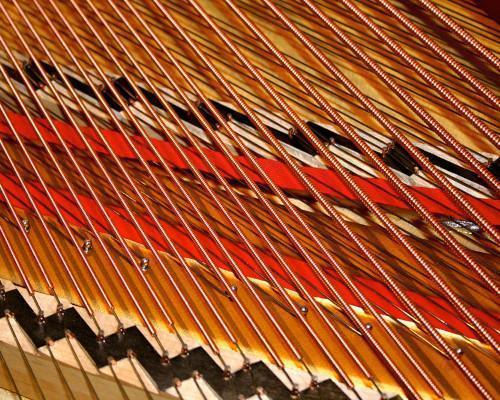
Researching Pianos - Piano Strings
Last month we learned that felt matters. The quality and make-up of the felt determines the impact point and subsequent character of the piano as the hammers strike the strings. In response to that, the strings themselves vibrate and begin the process of making sound. We learned in the discussion of string tension that there are on average 230 strings running the length of the piano, two thirds of which are plain wire and one third is copper wound bass strings.
When doing piano research, what matters regarding the strings? Isn’t wire just wire? Piano wire is made up of drawn [...]
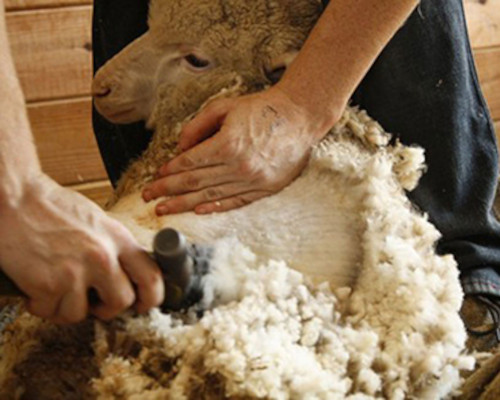
Researching Pianos - Hammer Felt Matters
I’ve heard this statement many times before: “I’m just doing my research on what piano to buy”. But what does this actually mean? What do people research when they say that they’re examining a piano? Isn’t a piano just a piano? They’re shiny, they have 88 keys with 3 pedals, right? While that is a correct statement, pianos are so much more than those elements. Perhaps it’s a better question to ask, “What differentiates one piano model from another?” rather than how they are the same.
Today we’re going to take a look into what I consider to be the single-most [...]
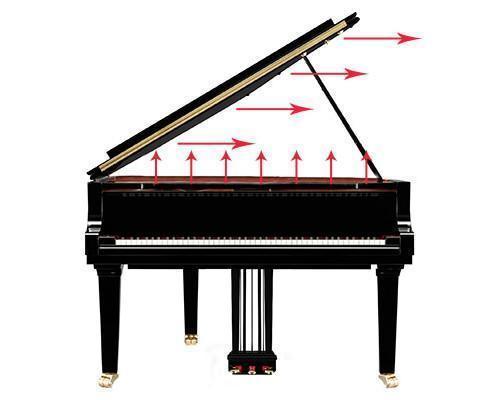
Optimizing Piano Acoustics At Home
“Just place the piano up against the wall”. It’s a common statement told to piano movers. But why should a piano be against a wall in the first place? Aside from the fact that the back of an upright piano is rather unsightly, let’s consider the placement of the piano. Although the perceived sound appears to emanate from everywhere on a piano, the predominant tone source is the soundboard – the large sheet of wood that amplifies the vibration from the strings. Piano strings make little sound by themselves without transferring the tone to the soundboard. If you think about [...]
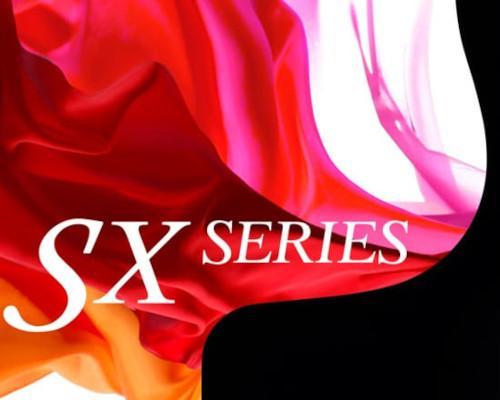
Yamaha SX Grand Pianos with ARE
Yamaha quietly introduced something this year at the NAMM show that caught my eye. It’s not a new process. In fact, it’s been going on since the 8th century with the Vikings in their ship building. Since the 1930’s, Scandinavian countries have also been experimenting with it. You might even benefit from it with the coffee beans that go into your brew. But it’s only been since the last decade that this has taken the guitar world by storm. What is it? The process is called torrefication (aka torrefaction). In its simplest form, it’s a type of roasting, which involves [...]
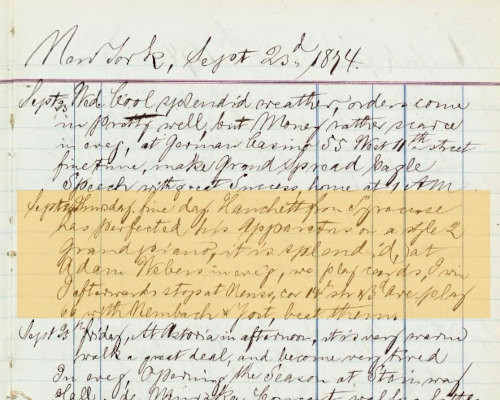
The Sostenuto Pedal
There has never been said any words in the piano industry that are more divisive than “But does it have a middle pedal?” Why are these words divisive? Because the middle pedal on the piano is the least used and yet most focused on in the piano industry. I’ve often told the story about one of the greatest jazz pianists in my city, when he was just signing the papers to purchase a beautiful grand piano, he stopped and turned to me and said, “Glen, I’ve just got to ask… What does the middle pedal do? I get asked because [...]
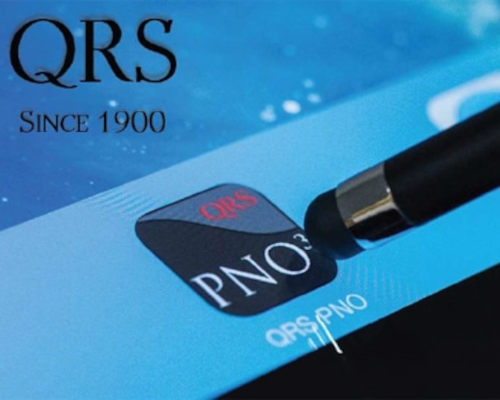
What's a Piano Cloud? QRS Music
You get your cup of coffee and log in to your computer. “Hmmm… not a lot of practicing from these students this week. Looks like Rachel is having problems with that new scale. Braden is having trouble with timing.” This is the new look of piano teaching in the 21st century.You get off work late and think to yourself, “All I want to do is relax on the couch and watch a movie like The Legend of 1900 or hear Billy Joel on the big screen and listen to it through my piano”. This too is the new look of [...]
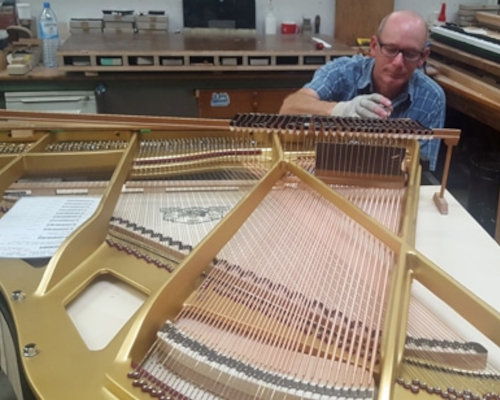
Who Is Grotrian?
The World Fair became The World Exposition which became Expo as we know it. I stumbled upon a book about the musical instruments from the world fair in the late 1800’s. It was said of Grotrian “There is no effort to produce them in great numbers, but rather to create in every one, as it passes through the factory, an instrument fit for the inspiration of great artists who have long accorded to its makers the highest place.” Of their experience, “It is said that nowhere in the world are there more veteran employees than in the factory of Grotrian.” [...]
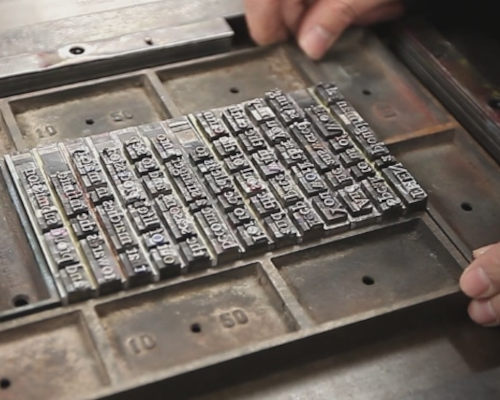
The Una Corda Pedal - The Soft Pedal
A few months ago we examined the mechanical and musical basics of the damper pedal. This month we’re going to look at how the una corda, also known as the soft pedal, works.
I was speaking with an older gentleman recently who used to be a typesetter for a newspaper, meaning that he would manually place letters in rows each day for the daily newspaper (pre-computer and pre-typewriter). Each of the letters in the alphabet was grouped together and were called “sorts”.
As the day progressed, depending on what the typesetting would require, you might run out of a certain letter, like [...]
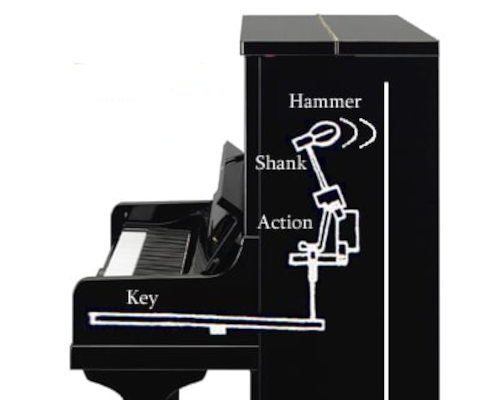
Why Upgrade to a Professional Level Piano?
Last month we looked at why upgrading happens from an electronic keyboard to a real piano. This month, we delve into the concept of why it is sometimes necessary to upgrade from one acoustic piano to another. Having been in sales, I’ve discussed this concept many times with parents shopping for a piano. The teacher has said, “your son/daughter is advancing and you need to consider upgrading your piano to something better”. This begs the question, “Why do we need to upgrade? And what’s inferior about my existing piano that makes it inadequate?”These are both valid questions. I need to [...]
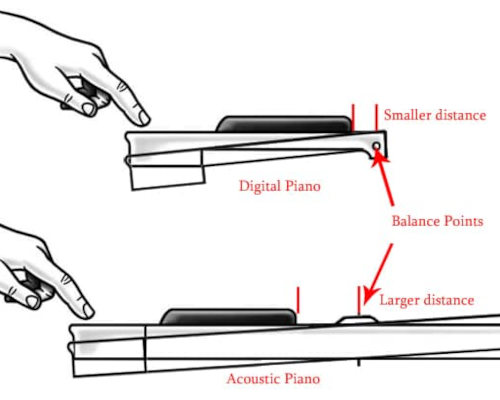
Why Upgrade from a Digital Piano?
The teacher has said “It’s time you start looking for a real piano and move up from a keyboard. You’ve outgrown this one”. Really? How does that happen? Just 2 years ago you bought this brand new 88 key weighted digital piano and now you’re being told that it will not suffice. They both have the same amount of keys and it has the same touch as a piano. Why do we need to upgrade? In order to answer that question, we need to look at the differences between acoustic piano (traditional piano with strings and hammers) and digital piano [...]
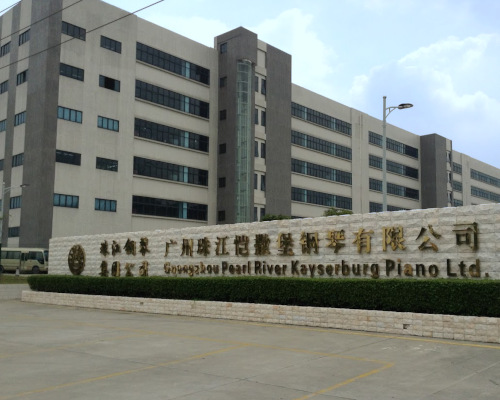
Visiting Pearl River Factory
On this latest trip to China, I managed to catch a glimpse into the transformation of Pearl River Piano. Already the largest piano company in the world manufacturing more than 130,000 pianos annually, Pearl River Piano has its sights set on even greater advancement.
One hundred thirty thousand pianos annually equates into about 400 pianos being manufactured per day. Imagine though what it must be like to produce 400 pianos daily. With roughly 225 tuning pins per piano, that’s 90,000 coils per day. Conservatively a piano contains 200 pounds of iron for each frame. That would be 80,000 lbs of iron [...]
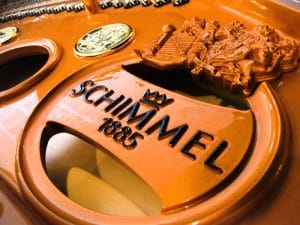
Pearl River and Schimmel Alliance
Recently I sat down with June Wang from Pearl River Piano Group and corresponded with Rob Slayman from Schimmel Piano to discuss their strategic alliance as I was curious how it had affected both companies. It was announced at NAMM 2016 that Pearl River had purchased a controlling interest in the Schimmel company.
Why do piano companies purchase other piano companies? We hear of company mergers in the news all the time. What is the impetus – the driving force for one piano company to acquire another piano company? If we paint with large brush strokes, on one side there is [...]
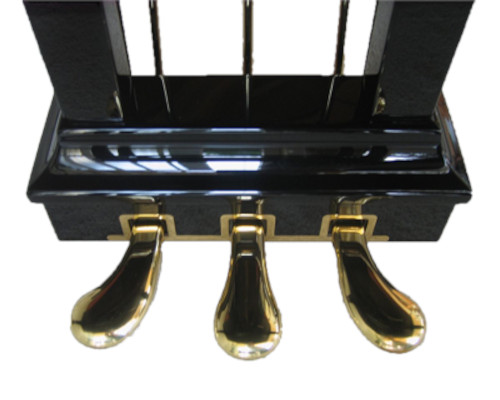
Musical and Mechanical Basics of the Damper (Sustain) Pedal
I remember teaching my kids how to drive a car. At first it’s a bit daunting putting a young adult in a 2 ton vehicle controlled primarily by a gas pedal. Over time, the confidence and competence increase. What remains somewhat of an accepted disconnect, however is HOW that process works. You put your foot on a small pedal and ‘magically’ the vehicle moves. Similarly, piano pedals are like that: if you step on the sustain pedal (the right pedal), the sound of the piano is transformed. Today, we’re going to delve into a bit more of the mechanical side [...]
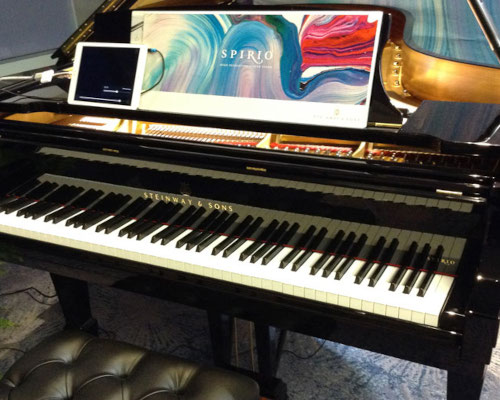
Player Pianos in the 21st Century
A Voice from the Past
“Step right up… See the amazing piano that plays by itself!” I can just hear the man at a trade show in the 1920’s. “Just push the pedals and this paper roll will play songs like Swanee and The Entertainer and Bicycle Built for Two.”
This invention in the late 1800’s was quite remarkable. It functions similarly to a harmonica in reverse. Rather than blowing through holes in a harmonica, the player piano sucks air through a perforated tracker bar. The paper roll has a punch-out hole position for every note on the piano. Through the use [...]
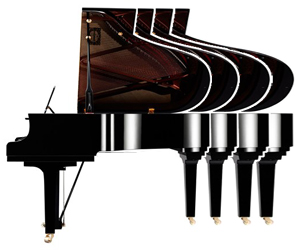
Piano Sizes ~ What Should I Buy?
I’ve heard this statement many times “I don’t want a concert grand, I’m looking for more of a baby grand”. To many, this is a completely normal statement. For those who have been around pianos, the translation is more like this: I’m not interested in a limousine, I’m looking for a subcompact car”. I believe that there is a lack of knowledge why the former statement is prevalent. People either see a massive piano on a stage or they see a piano in a home. VOILA! 2 sizes of pianos – concert grand and baby grand. When you start to [...]
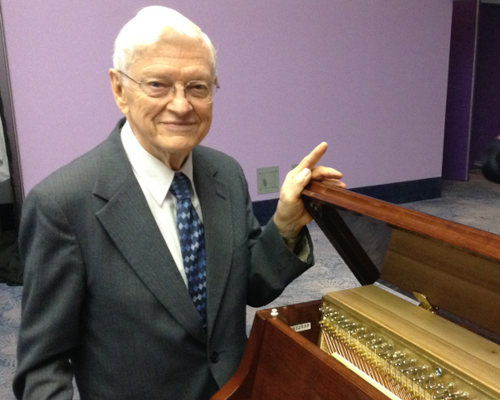
An Interview with Charles Walter Piano Company
Meet Mr. Charles Walter, CEO of the company which bears his name. I had the privilege of speaking with him both at the last music trade show (NAMM 2016) and also a few days ago. I enjoy meeting those who are directly involved not only in piano make-up and design but those who are living legends. The Walter Piano Company is the oldest family run American piano company in existence today. And when I say family run, I mean that each of the Charles Walter pianos that come out of the production facility has been manufactured in part by members [...]
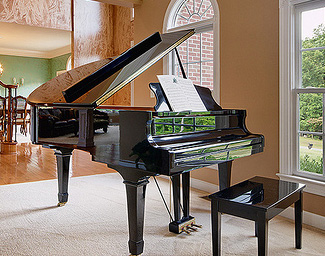
Making the Perfect Piano Black
Have you ever heard someone describe an object as being “jet black”? Jet is derived from the French word “jaiet”, a process that dates back to the 1300’s where lignite (a type of coal) was polished to a deep sheen. It was referenced as the benchmark for black as early as the 1700’s. But jet black has been overtaken by “piano black” as the example for the deepest, darkest, smoothest finish of comparison. In recent decades, with the advancement of technology and engineering, piano finishes have been perfected and there is now an association with “modern piano” as being black. [...]
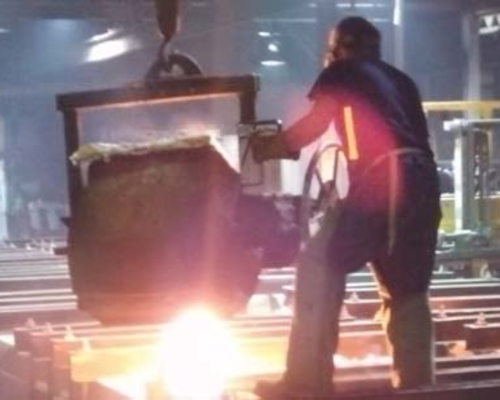
Casting Iron Piano Frames
Every piano has one. It is the backbone to structural integrity. It’s also what gives a piano most of its weight. What is it? Commonly called the frame, harp or plate, this iron mass in the piano withstands the 19+ tons of string tension.While iron reinforcement pieces were introduced into the piano by the year 1799, it wasn’t until 1825 that a full cast iron frame was patented by a man named Alpheus Babcock (The Piano: An Encyclopedia. Palmieri). All of the piano manufacturing world then saw the great advantage of the implementation of iron, and have incorporated iron frames [...]
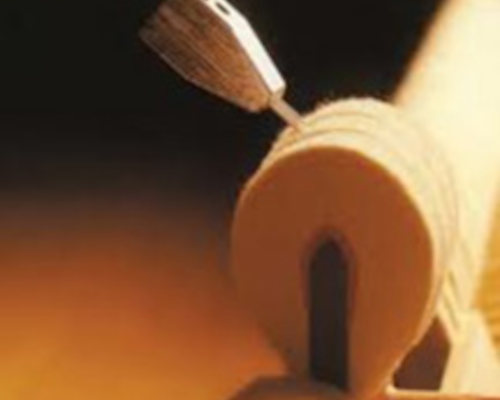
The Art of Piano Voicing
I had the full intention of writing a blog on piano voicing and then suddenly realized that there are 3 completely valid meanings to piano voicing. The first meaning of voicing refers to chord voicing which denotes how you spread out the notes of a chord on the piano (quite often in the jazz idiom). The second meaning, as it refers to piano playing and pedagogy means making the melody line stand above the accompaniment. You voice the melody to be more audible than the rest of the notes you’re playing. The third definition however, refers to the technical aspect [...]