When doing research on pianos, what role does the soundboard play? After a key is struck on the piano, the hammer is activated to strike against the strings. The vibration of the strings, in turn transfers the vibration through the bridge to the soundboard. It’s the job of the soundboard to act as a transducer, transforming the vibrations of the strings into audible waves of sound. While we casually talk about the soundboard being an amplifier, technically speaking an amplifier ADDS energy to multiply the sound source whereas a soundboard inherently transforms and radiates energy into sound waves. If you think of a skin of a drum where the rim is attached around the edges, so too the piano soundboard vibrates freely in the middle and the edges are affixed to the rim of the piano. This vibration from the board allows us to hear the piano, without which the string vibration would be but a whisper.
Well over 100 years ago, spruce became the popular wood of choice for piano soundboards. Possibly taking the lead from violin and harpsichord makers which had existed for centuries, the soundboard material utilizes tone wood made from spruce due to its combination of elasticity for vibration and strength. I’ve been wading through a book from 1916 called “A Treatise on the Art of Pianoforte Construction” where the author gives an overview of piano making. Interesting to note is the experimentation of other substances that were still being considered for soundboards. “Most woods and metals would serve as resonators, with varying degrees of efficiency.
Among the metals, iron, copper, and aluminium have been tried, but only experimentally; the first results seem never to have warranted a continuous departure from the common practice.” ~ the common practice of using cone-bearing trees such as spruce.
Yamaha makes a very interesting point that spruce not only produces lovely tones but also inhibits unwanted frequencies:
“If it were only a matter of loudly amplifying the sound produced when the hammers strike the strings, a metal plate would have been much more efficient. So why is the soundboard made from wood? The answer is that, unlike metal, which amplifies both low and high frequency sounds in the same way, wood amplifies only the lower-frequency sounds. For the higher frequencies, it does the opposite: it cuts them off…In other words, the soundboard is a “board that transmits vibrations,” while at the same time, it is in a certain sense, a “board that stops vibrations.” What makes the spruce family and especially Alaskan (Sitka) spruce, so highly valued as soundboard materials is that these species have the property of absorbing the higher overtones more effectively. They transmit only the sounds that we perceive as round and mellow in a rich fashion.”
In essence then, the soundboard acts like a sort of filter. It may not be the only substance that could be used as a soundboard but history confirms that it is by far the most excitable, resonant and strongest wood in its class to resist the pressure of piano string tension and simultaneously filtering desired frequencies of sound. Since the early 1900’s, technical data has proven the point that spruce will remain the soundboard material of choice.
If soundboards are all made from spruce with modern manufacturing, what then are the differences with regards to doing piano research? While we could discuss thicknesses, how they are tapered from the edge to the middle, how many supporting ribs they have on the back or even grain orientation, by far the biggest discussion presently is about a solid or laminated soundboard.
Solid vs. Laminate
A solid soundboard is one that is made from solid planks of wood. A laminated soundboard is one comprised of layers of wood. It has been referred to in many different ways such as surface tension soundboard, multi-ply soundboard, meniscus soundboard but the structure is the same – glued layers of wood. The word laminated seems to have negative connotations attached to it. When we think of laminated wood, we hear the word plywood, which is inexpensive building sheets. Laminate also refers to inexpensive flooring. So why would laminate be used in a piano for a soundboard? Let me first ask you a question. If you were a piano manufacturer, which would be easier to construct, gluing planks of wood together or peeling thin layers of veneers and then pressing them together evenly under a few hundred pounds of pressure to form a homogenous board? The laminated soundboard is much more difficult to make. If having a solid soundboard is perceived more desirable and the laminated soundboard is more difficult to manufacture, why persist in making them? According to many logging companies and even luthiers, the supply of tone wood is dwindling rapidly. In fact, Guitar Player magazine stated over a decade ago “Sitka spruce, the wood used for the vast majority of acoustic guitar, piano, violin, and other musical-instrument soundboards—is being harvested at such a rate from the Southeast Alaskan forests where it grows that the end of the instrument-quality supply is in sight.” Initiating alternatives is necessary for continued manufacturing to keep piano prices reasonable. Some thoughts regarding solid and laminate soundboards:
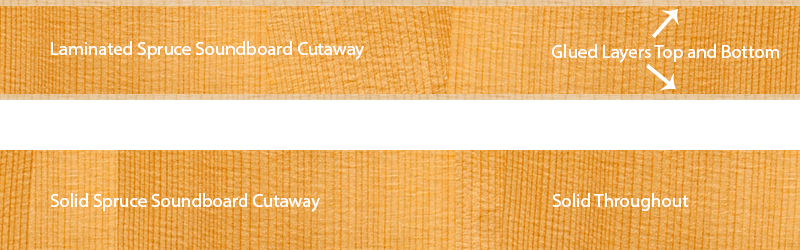
Solid soundboards
– historic, traditional method of making piano soundboards from planks
– wasteful in resources with quarter sawn wood
– difficult to sustain on mass scale utilizing close grain wood found on 100+ year old trees
– difficult to create consistency for close grain clear wood from one piano to the next
– as supply dwindles, cost of logging increases solid wood soundboards
Laminated soundboards
– environmentally friendly
– sustainable on large scale manufacturing
– more consistent end result
– center core wood doesn’t need to be cosmetically beautiful, therefore less wastage
– greater structural integrity
Over the past few decades, I’ve witnessed the development of laminated soundboards. Some of the earliest experiments produced some disastrous results. Not so today. In fact, I’ve recently played pianos and had to quite often ask if the soundboard was laminated. Obviously it’s doing its job correctly of sound transmission if I needed to ask. Many have posed the question “But why do high end pianos not have laminated soundboards?” I believe that this is in part a product of scale and economics mixed with tradition and superiority. Since high end pianos only represent a tiny fraction of global piano sales, it is economically viable to account for a solid soundboard. But it is also unnecessary to build the machinery to develop laminated boards when each boutique maker is not producing 10’s of thousands of pianos annually. In the piano culture, there’s this fascination with “solid” giving off the connotations of being sturdy or contain virtues of purity. I remember employing a French polisher who once educated me many years ago when I blurted out some remark about solid wood furniture. His swift response stopped me and corrected me instantly when he replied “You’re showing your ignorance. Don’t you know that all of the best antiques of the world contain beautiful veneers?” Interesting to note are the words of the man who wrote the patent for Steinway’s tapered soundboards. In a paper written a few years later in 1940, Paul Bilhuber, CEO and engineer for Steinway writes “This experimentation [for piano soundboards] has involved a rather complete investigation of materials and of possible variations in structure. No material of any promise has been overlooked. In addition to suitable varieties of woods, an attempt has been made to use such widely differing materials as metals, parchment, and plywood, both individually and in various combinations…The net result was that none of these radical designs contributed any important improvements in piano tone quality.” Notice that plywood (laminated) wood was mentioned and that it didn’t IMPROVE the current soundboard. In 1940, limited resources of forests were not in question. The pursuit of better piano tone was the objective. But today, the question remains, with modern technology and development of laminated woods, will it be on par with a solid soundboard? The only answer I can think of in piano design is that less is more – less layers possibly inhibiting sound transference is better.
Most parts of the piano are glued together in layers – the tuning pinblock, the rim of any grand piano, the key bed, support beams and cabinet parts. To that end, we embrace the advantages of structure, reinforcing cross grain lamination of layers. When it comes to sound, however, we must use our ears – regardless of material. When doing your piano research, I would ask that you suspend judgement about how many support ribs it has, whether it’s tapered, or hand scraped, or even notched to the inner rim. Soundboard technology is a much greater science than just a board – it’s a system of acoustics fully integrated with the piano so that the average listener will not be able to isolate its importance. But I will give 4 points to consider when evaluating a piano:
Sustain – As mentioned in previous articles, no part of the piano acts in isolation. But working in tandem, a great piano should contain great sustain. Lack of sustain can come from the shape of the hammers, the bridge but also the soundboard and ribs. From bottom to top notes, the soundboard should carry and sustain tone for many seconds, slowly and gradually dying away. Abrupt drop off in tone is never desirable in a piano. Conversely, I’ve played some pianos I would describe like a calm lake, the surface of the water, smooth as glass. When playing notes, it responds like tossing stones in the water, the rippled waves interrupting the clear glass. You can follow those waves as far as you can see. That elusive sustain is magic.
Color – While the spruce soundboard does, in fact filter frequencies of the steel strings, you also want to achieve desirable color that is uniform throughout. Sometimes you’ll find piano tone or color that is too strident in the bass or treble. While this could also be a product of harshness of hammer or string design, this could also be part of the soundboard. Listen for uniformity and complimentary tone in every octave, especially for notes that stick out.
Blind spots – Sometimes a piano will have a zone I would describe as a blind spot. You’ll be playing and all of a sudden, you hit a “thunk” – no substantial tone in one area of the piano. Whether it be the design, the manufacturing or the wood itself, there sometimes is one area where the piano doesn’t sing.
Unwanted vibrations – They come from various sources – strings that have unsuitable overtones, a hammer that has a sharp edge, an agraffe that doesn’t have a proper termination point, a sympathetic overtone caused from a hinge, pianos sometimes develop unwanted vibrations. While the aforementioned things all can be adjusted, having an unwanted vibration in the soundboard is a trickier correction. Listen for overtones, vibrations that are not congruent with the tone you’re playing.
Soundboards in their simplest form magnify the piano tone. It’s the implementation that’s incredibly complex. It involves a combination of ratios and tolerances that comprise the “recipe” or scale design of each manufacturer. Rather than looking at specifications, do lots of listening. If you don’t feel qualified in the area of piano listening, I suspect you haven’t been around that many pianos. It’s been my observation that even novice pianists can still hear the differences among pianos. My advice when it comes to soundboards is to listen again and again as well as compare various models in your price range.
Important to note are some of the independent soundboard makers such as Bolduc and Ciresa. Piano Price Point also did an interview with Bolduc which gives more information about the making of piano soundboards. Be sure and read The Troublesome Truth About Sitka Spruce which speaks to the disappearing supply of sitka spruce for soundboards and how we need to be careful stewards of natural resources.
MORE PIANO ARTICLES
You’ve been playing your piano for years now and the time has come to seriously consider downsizing the house and move into a condo. But what do you do with the piano? You love your piano and can’t imagine life without it and besides, you absolutely hate the idea of playing a digital keyboard. Many people don’t know that you can add digital functionality without compromising your existing piano. Yes, it is completely possible to ...
Many years ago, I remember seeing a piano in a museum similar to the one shown above (built in 1787 by Christian Gottlob Hubert. On display at Germanisches Nationalmuseum - Nuremberg, Germany). I have often wondered why acoustic portable pianos never really took off. Although we've seen more portable keyboard instruments like harpsichords, accordions or electronic keyboards, they operate completely different from a traditional piano in that they either pluck the strings, use air with ...
This was the first year since covid that the National Association of Music Merchants (NAMM) trade show was back to its regular January date and, in fact the first show where it felt back to normal. How was it? To answer that, I'm going quickly review the piano market over the last few years. Piano sales boomed during covid. Think about it - everyone was at home and with time on their hands, many turned ...
I’ve often wondered when the business model of piano buying would start to change. It seems like we feel comfortable purchasing everything from toothpaste to tires online and yet pianos are one thing that you still buy in a store. Well some of that is about to change. After speaking with Larry Caruso from Caruso Piano, they’re launching a brand of piano made specifically for online ordering. It’s called
Sonnova. I recently had the pleasure ...
The thought of buying a piano can be exciting but it can also be a bit intimidating or daunting, especially if you don’t know anything about them. But have no fear, because at Piano Price Point, we’ve compiled so much of the data and written articles to make your job easier. To narrow down the scope of buying a piano, you first need to decide what kind of piano you’re looking for. Ask yourself these ...
Money, apparently
does grow on trees or at least in ancient times it did. It's been recorded that rare tree sap was used as a form of payment for tax because it was deemed so valuable. This sap from the tree was harvested and refined into lacquer with incredible clarity and sheen. Many thousands of years ago, it was reserved for imperial palaces, religious temples and shrines. Early
examples have been dated to 7000BC. It ...